A New Chapter in the Encapsulation of LED Displays: What's the Difference between SMD and COB Technologies?
With the rapid development of the commercial display industry in recent years, LED display screens, as an indispensable part of it, have witnessed rapid technological innovations day by day. Among numerous technologies, SMD (Surface Mount Device) packaging technology and COB (Chip on Board) packaging technology are particularly noticeable. Today, we will analyze the differences between these two technologies in a simple and easy-to-understand way to show you their respective charms.
First of all, let's start from the technical aspect. SMD packaging technology is a form of packaging for electronic components. SMD, short for Surface Mounted Device, means surface-mounted device. It is a widely used technology in the electronics manufacturing industry for packaging integrated circuit chips or other electronic components so that they can be directly installed on the surface of a PCB (Printed Circuit Board).
Main Features:
Small Size: The components packaged by SMD are small in size, enabling high-density integration, which is beneficial for designing miniaturized and lightweight electronic products.
Light Weight: Since SMD packaged components don't require pins, the overall structure is lightweight, suitable for applications that require light weight.
Good High-Frequency Characteristics: The short pins and short connection paths of SMD packaged components help to reduce inductance and resistance, improving high-frequency performance.
Convenient for Automated Production: SMD packaged components are suitable for production by automated placement machines, improving production efficiency and quality stability.
Good Thermal Performance: SMD packaged components are in direct contact with the surface of the PCB, which is beneficial for heat dissipation and improves the thermal performance of the components.
Easy to Repair and Maintain: The surface mounting method of SMD packaged components makes it more convenient to repair and replace components.
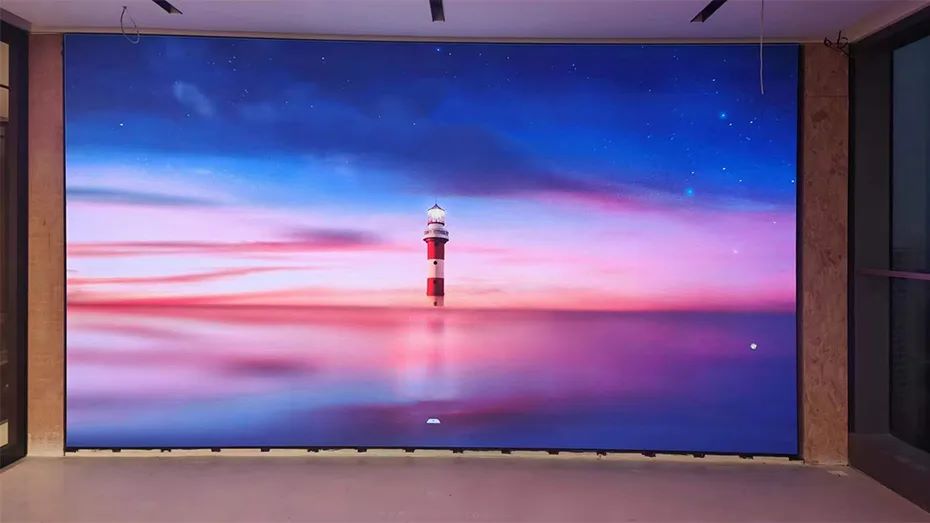
Packaging Types: There are various types of SMD packaging, including SOIC, QFN, BGA, LGA, etc. Each packaging type has its specific advantages and applicable scenarios.
Technological Development: Since its introduction, SMD packaging technology has developed into one of the mainstream packaging technologies in the electronics manufacturing industry. With the progress of science and technology and the demands of the market, SMD packaging technology is also constantly evolving to meet the needs of higher performance, smaller size, and lower cost.
COB packaging technology, whose full name is Chip on Board, is a packaging technology that directly solders the chips onto the PCB (Printed Circuit Board). This technology is mainly used to solve the heat dissipation problem of LEDs and achieve close integration between the chips and the circuit board.
Technical Principle: In COB packaging, the bare chips are adhered to the interconnect substrate with conductive or non-conductive adhesives, and then wire bonding is carried out to realize their electrical connections. During the packaging process, if the bare chips are directly exposed to the air, they are prone to be contaminated or damaged by humans. Therefore, usually, the chips and the bonding wires are encapsulated with glue to form what is called a "soft encapsulation".
Technical Features: Compact Packaging: Since the packaging and the PCB are combined together, the chip size can be greatly reduced, the integration degree can be improved, the circuit design can be optimized, the circuit complexity can be reduced, and the system stability can be enhanced.
Good Stability: The chips are directly soldered onto the PCB, so they have good vibration resistance and impact resistance. They can also remain stable under harsh environments such as high temperature and humidity, prolonging the product life.
Good Thermal Conductivity: By using thermally conductive glue between the chips and the PCB, the heat dissipation effect can be effectively improved, the impact of heat on the chips can be reduced, and the service life of the chips can be increased.
Low Manufacturing Cost: Since there are no pins, some complex processes of connectors and pins in the manufacturing process are saved, reducing the preparation cost. At the same time, automated production can be realized, reducing labor costs and improving manufacturing efficiency.
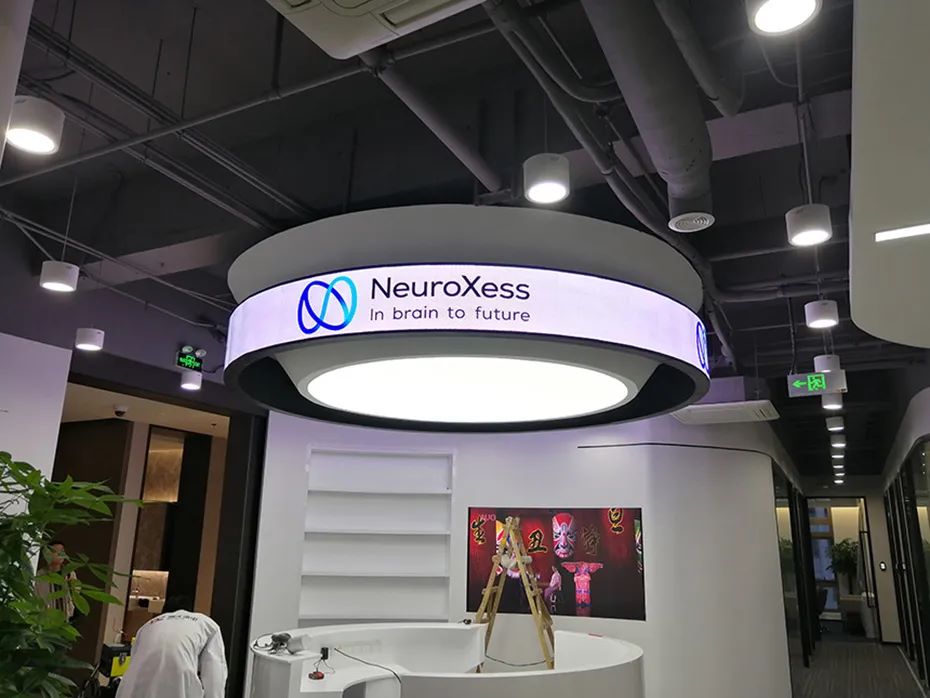
Precautions:
- Difficult to Repair: Since the chips are directly soldered to the PCB, it is impossible to disassemble or replace the chips individually. Generally, the entire PCB needs to be replaced, which increases the cost and difficulty of repair.
- Reliability Dilemma: The chips are embedded in the adhesive. During the disassembly process, the micro-disassembly frame is easily damaged, which may cause a shortage of solder pads and affect the production tendency.
High Environmental Requirements in the Production Process: The COB packaging process does not allow dust, static electricity and other pollution factors in the workshop environment. Otherwise, it is likely to lead to an increase in the failure rate.
Overall, the COB packaging technology is a cost-effective and excellent technology with broad application potential in the field of intelligent electronics. With the further improvement of the technology and the expansion of application scenarios, the COB packaging technology will continue to play an important role.
So, what exactly are the differences between these two technologies?
Visual Experience: With the characteristics of surface light sources, COB display screens bring a more delicate and uniform visual experience to the audience. Compared with the point light sources of SMD, COB has more vivid color performance and better detail processing, and is more suitable for long-term and close-up viewing.
Stability and Maintainability: Although SMD display screens are convenient for on-site repair, their overall protection is relatively weak and they are easily affected by the external environment. On the other hand, COB display screens, due to their overall packaging design, have a higher protection level and better waterproof and dustproof performance. However, it should be noted that once a fault occurs, COB display screens usually need to be returned to the factory for repair.
Power Consumption and Energy Efficiency: Since COB adopts an unobstructed flip-chip process, its light source efficiency is higher and the power consumption is lower under the same brightness, saving electricity bills for users.
Cost and Development: SMD packaging technology is widely used in the market due to its high maturity and low production cost. Although COB technology is theoretically lower in cost, due to its complex production process and relatively low yield rate, its actual cost is still relatively high at present. However, with the continuous progress of technology and the expansion of production capacity, the cost of COB is expected to be further reduced.
Nowadays, in the commercial display market, COB and SMD packaging technologies each have their own merits. With the continuous growth of the demand for high-definition display, Micro LED display products with higher pixel density are gradually favored by the market. And COB technology, with its high-integration packaging characteristics, has become one of the key technologies to achieve high pixel density of Micro LED. Meanwhile, with the continuous narrowing of the dot pitch of LED screens, the cost advantage of COB technology is becoming more and more prominent.
In the future, with the continuous progress of technology and the continuous maturity of the market, COB and SMD packaging technologies will continue to play an important role in the commercial display industry. We have reason to believe that in the near future, these two technologies will jointly promote the commercial display industry to develop in the directions of higher definition, more intelligence and greater environmental protection. Let's wait and see and witness this exciting moment together!